The selection of the installation site is most overlooked by the staff. Often after the compressor is purchased, you can find a location at random and use it immediately after piping. There is no prior planning at all. Little do they know that such a sloppy result will cause future compressor failures and maintenance difficulties and poor compressed air quality. Therefore, choosing a good installation place is a prerequisite for the correct use of the air compressor system [12]. 1. A wide and well-lit place is required to facilitate operation and maintenance. 2. The relative humidity of the air should be low, less dust, clean and well ventilated. 3. The ambient temperature must be lower than 40℃, because the higher the ambient temperature, the smaller the output air volume of the compressor. 4. If the factory environment is poor and there is a lot of dust, pre-filter equipment must be installed. 5. Reserve access roads, and those who meet the conditions can install cranes to facilitate maintenance. 6. Reserve space for maintenance, and there must be a distance of at least 70 cm between the compressor and the wall. 7. The compressor should be at least one meter away from the headspace.
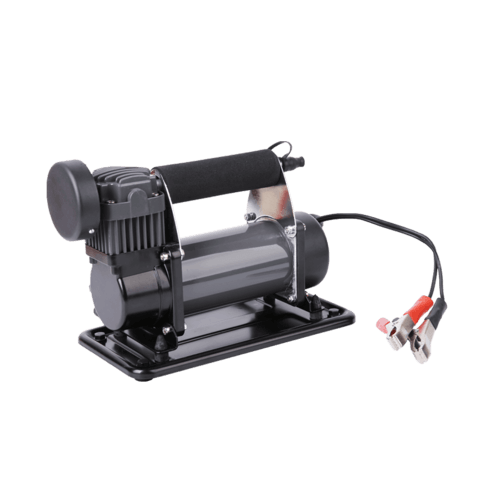
7. If the air consumption of the system is very large and the time is short, and the instantaneous air consumption changes greatly, an air storage tank should be installed as a buffer (its capacity should be greater than or equal to 20% of the maximum instantaneous air volume), which can reduce The frequency of frequent loading or unloading of the compressor unit reduces the number of actions of the control elements, which is of great benefit to maintaining the reliability of the compressor. Under normal circumstances, a gas storage tank with a capacity of 20% of the displacement can be selected. 8. For compressed air with system pressure below 1.5MPa, the flow velocity in the delivery pipe must be below 15m/sec to avoid excessive pressure drop. 9. Minimize the use of elbows and various valves in the pipeline to reduce pressure loss. 10. The ideal piping is that the main line surrounds the entire plant, so that compressed air in both directions can be obtained at any position. For example, when the gas consumption of a branch line suddenly increases, the pressure drop can be reduced. In addition, appropriate valves are arranged on the ring-shaped trunk line to facilitate maintenance and cut-off.